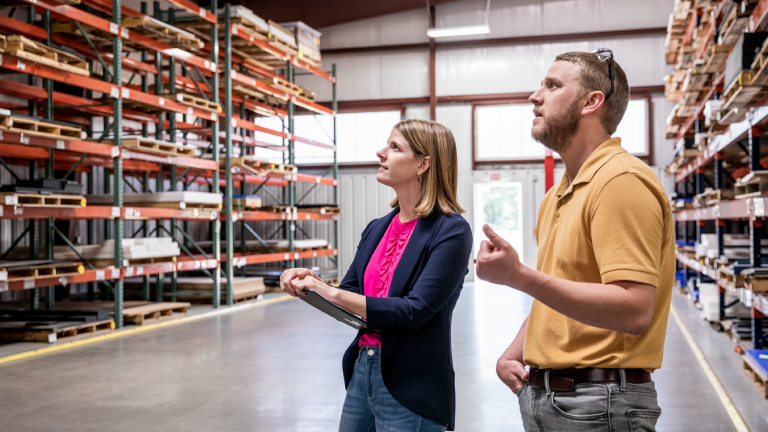
In the world of manufacturing, efficiency and productivity are key to success. Finding ways to optimize the production process can yield significant benefits in terms of time and cost savings, as well as improved product quality and performance. One way to achieve this is by using performance plastics in product design and specification.
Why would you select performance plastics for your parts? Performance plastics often require less frequent replacement and maintenance, reducing downtime and material waste. Performance plastics can withstand harsh chemicals, extreme temperatures, and high pressure, which contributes to a longer lifespan for the product and reducing the need for frequent replacements.
Engineers can take advantage of the unique properties of performance plastics to create designs that are lighter-weight, more durable, and more resistant to wear and tear. This often results in reduced raw material costs, improved product performance, and improved production processes.
To fully take advantage of the benefits of high-performance plastics, it’s important to work with a machine shop that has the expertise and experience necessary to deliver quality results. For over 40 years, Konrady Plastics has been a trusted partner to manufacturers in a variety of industries. Their quality-driven approach and attention to detail have resulted in a less than 1% return rate for their products.
Konrady Plastics responsive approach ensures that customers are kept up-to-date throughout the production process, from the initial quotation to timely delivery. They work closely with their clients to understand their production needs.
It’s time to consider performance plastics to lower costs, increase efficiency, and optimize production. Call Konrady Plastics if you’re interested in learning more.